

Lean Production
Lean Production (Schlanke Produktion) hat sich in der Praxis etabliert, da es viele Unternehmen wettbewerbsfähiger und effektiver gemacht hat. Lean Production ist ein Konzept zur Produktionsorganisation und wird auch oft mit den Worten „weniger ist mehr“ beschrieben. Der klare Fokus liegt auf der Verbesserungen der Durchlaufzeiten und Prozessqualität entlang des Produktionsprozesses bei gleichzeitiger Kostenminimierung. Vermeidung von Verschwendung und konsequenter Kunden- und Flussorientierung – erlauben, die Produktqualität zusätzlich zu steigern oder zumindest auf gewohnt hohem Niveau zu halten.
Bei Lean Production soll die Fertigung an die Bedürfnisse der Kunden ausgerichtet werden, Aktivitäten die nicht wertschöpfend sind, für die der Kunde nicht bereit ist zu zahlen, müssen eliminiert werden. Ziel ist es, jegliche Art von Verschwendung entlang der Wertschöpfungskette zu vermeiden.
Dienstleistungen
Der Waste Walk ist ein Führungsinstrument mit der Fokussierung auf die kontinuierliche Verbesserung und aktivem Coaching der Mitarbeiter. Ursprünglich für Führungskräfte und Manager entwickelt, wird diese Methode mittlerweile jedoch auf allen Hierarchieebenen angewendet. Das Geschehen vor Ort wird beobachtet und mit den Mitarbeitern vor Ort gesprochen.
Unser Leistungsspektrum bei der Durchführung von Waste Walks umfasst Folgendes:
- Strukturiertes Vorgehen zur Analyse der aktuellen Situation
- Grundlagenschulung Gemba Walk
- Betriebliche Herausforderungen präzisieren
- Schwerpunktthemen auswählen
- Durchführung „go & see“- „sehen lernen“
- Identifikation von Verbesserungspotenzialen unter Einbezug der Mitarbeiter
- Integration in die betrieblichen Regelkreise
- Durchführung analoger Walks in Ihrem Unternehmen wie ebenso digitaler Walks mittels Smart Glasses
6S ist der Grundbaustein im Unternehmen, um Prozesse an der Basis, im Produktions- und Montagebereich, unter Einbindung aller beteiligten Mitarbeiter, zu optimieren. Optimal gestaltete Arbeitsplätze und Abläufe entstehen durch die Definition von Standards. Ohne 6S im Lager, der Produktion und im Büro nehmen die Verschwendungsanteile im Laufe der Jahre weiter zu.
Unser Leistungsspektrum beim Aufbau von Produktionssystemen umfasst:
- Grundlagenschulung im Rahmen einer Informationsveranstaltung zur 6S Methode
- Ist-Analyse durchführen zur Ermittlung der Ausgangslage vor Ort
- Impulsgebung durch Benchmark Projekte
- Maßnahmenverfolgung und Sicherstellung wirksamer 6S Arbeitskreise
- Coaching und Qualifizierung der Mitarbeiter
- Ausgestaltung sinnvoller Überwachungsmethoden (6S Audits)
- Beratung bei der Auswahl sinnvoller Standards
- Begleitung, Moderation und „Training on the job“ von 6S-Teams
- Beratung bei der Verknüpfung der 6S Methode mit weiteren internen Q-Methoden und Lean Management Methoden
- In jeder Phase der Integration eine enge Zusammenarbeit mit den Fachleuten
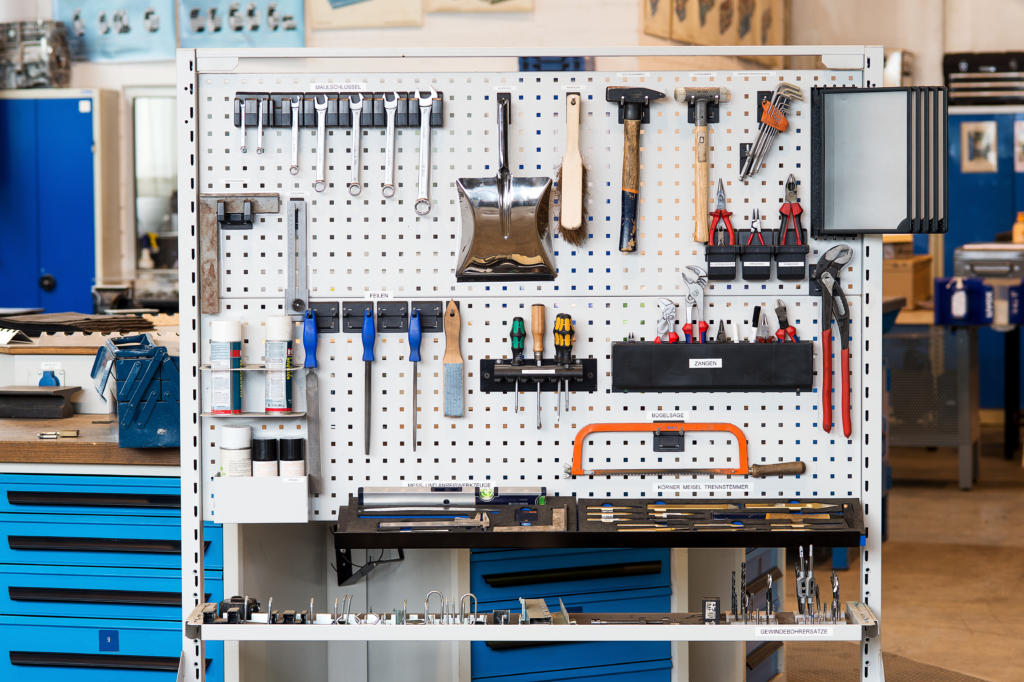
Total Productive Maintenance umfasst die effektive Nutzung der Produktionsanlagen durch ganzheitliche Betrachtung der Verantwortung für routinemäßige Instandhaltungsaufgaben. Die Gewährleistung einer durchgängigen Kunden- und Wettbewerbsorientierung führt zu hohen Anforderungen an die Produktivität und Flexibilität von Anlagensystemen und konkretisiert sich in einem hochgradigen Anforderungsprofil an die Verfügbarkeit und an die Umrüstfähigkeit der Anlagensysteme.
Unser Leistungsspektrum bei der Einführung von TPM umfasst Folgendes:
- Durchführung einer TPM-Ist-Analyse zur Ermittlung der Ausgangslage und der Identifizierung möglicher Potenziale
- Verzahnung von Produktion und Instandhaltung
- Ableiten von Aufgaben und Kompetenzen und Verantwortung
- Erstellen von Regelkreisen (Kanban Board / T- Karten Boards)
- Verschwendungsfreiheit: null Fehler, null Unfälle, null Ausfälle, null Leistungsverluste
- Messbarkeitssteigerung der Anlageneffektivität (OEE)
- Hilfestellung bei der Etablierung einer Kennzahlensystematik zur Erfolgsbewertung
SMED steht für „Single Minute Exchange of Die“ und beschreibt eine Methode zur Reduzierung von Rüstzeiten. Ziel ist es, dass das Umrüsten einer Anlage oder Maschine von Produkt A auf Produkt B (= Produktwechsel) im einstelligen Minutenbereich geschieht. Durch organisatorische als auch durch technische Maßnahmen soll die Umrüstzeit auf weniger als 10 Minuten gebracht werden.
Unser Leistungsspektrum bei der Einführung von SMED umfasst Folgendes:
- Die klare Identifizierbarkeit wertsteigernder, nicht-wertsteigernder und kostensteigernder Tätigkeiten
- Die Unterscheidung zwischen internem und externem Rüsten
- Rüstparameter als Voraussetzung für Qualität und stabile Prozesse
- Flexibilisierung der Produktionseinrichtungen durch Rüstzeit-Reduktion
- Vor- und Nachteile kleiner Losgrößen
- Verkürzung der Maschinen- Stillstandzeiten
- regelmäßiges Wiederholen dieser Schritte für einen kontinuierlichen Verbesserungsprozess (KVP)
Lean Logistik bedeutet alle Aktivitäten in der Logistik zu identifizieren und zu eliminieren, die keinen Mehrwert bringen. “Durch weniger von allem mehr erreichen”. Weniger Aufwand, weniger Zubehör, weniger Platz, weniger Kosten und weniger Zeit ist das Ziel. Auf der einen Seite gilt es dem Kundenwunsch nach Effizienz, Pünktlichkeit und Transparenz nachzukommen. Auf der anderen Seite gilt es, das eigene Unternehmen profitabel und wettbewerbsfähig am Markt zu positionieren. Optimalerweise vereint Lean Logistik beide Ziele in einem schlanken Prozess.
Unser Leistungsspektrum bei der Einführung von Lean Logistik umfasst Folgendes:
- Prozess und Wertstromaufnahme
- Identifizieren der Aktivitäten, die einen Mehrwert für den Kunden haben
- Verschwendung erkennen und gleichzeitig Verbesserungsmöglichkeiten finden
- Erstellen eines neuen optimierten Prozessablaufs (Wertstromdesgin)
- Pull-Strategien anwenden zur Bestandsminimierung
- Neue Prozesse standardisieren und auf Veränderungen reagieren
- Produktionsprozesssteuerung mittels Kanban
- Demand-Driven Material Requirements Planning (DDMRP)
- Behälterstandardisierung
- Schnittstellenanalyse
Durch die Visualisierung des Wertstroms werden die Prozesse in ihrer Komplexität über alle Fachbereiche hinweg transparent dargestellt. Silo- und Abteilungsdenken wird aufgebrochen. Selbst komplexe Wertströme lassen sich auf verschiedenen Detailebenen oder Wertstromabschnitten abbilden und abstimmen.
Unser Leistungsspektrum im Rahmen der Wertstromanalyse und-design umfasst Folgendes:
- Aufnahme und Visualisierung des Wertstroms
- Mengengerüst erstellen (Wertstrom- / Produktauswahl)
- Kundentakt definieren
- Ist-Zustand aufnehmen
- Potenziale aufzeigen
- Aufwand Nutzen Darstellung
- ROI Berechnungen
- Out of the Box Denken (Walt Disney)
- Generierung von Greenfield- Ansätzen
- Entwicklung eines optimierten Soll-Prozesses
- Definition einer Roadmap
Mit Shopfloor Management ist das Führen direkt am Ort des Geschehens gemeint. Der Begriff Shopfloor Management wurde durch Toyota geprägt und ist im Zusammenhang mit dem Toyota Produktionssystem der Dreh- und Angelpunkt für die Sicherstellung verschwendungsfreier Produktherstellungsprozesse. Durch einen organisierten und kaskadierten Kommunikationsablauf kommt die Führungskraft in Ihre eigentliche Rolle; dem Führen der Mitarbeitenden und der Fokussierung auf die Wertschöpfung. Durch visuelle Instrumente und eine geordnete Kommunikation werden erreichte Ergebnisse kontinuierlich bewertet und wenn notwendig KVP-Maßnahmen eingeleitet.
Unser Leistungsspektrum im Rahmen des Shopfloor Managements umfasst Folgendes:
- Etablierung Kommunikations- und Eskalationskaskade
- Trainieren der Problemlösekompetenz am Ort der Wertschöpfung
- Installation von SFM Coaches über 2nd Coach Ansatz
- Konsistente Ausrichtung aller Teilbereiche auf die Unternehmensziele
- Transparenz von Soll-/ Ist – Zuständen und Trends
- Das Denken in Regelkreisen (PDCA/ Problemlösung)
- Versachlichung von Diskussionen
- Effiziente und zielgerichtete Kommunikation in und zwischen den Teams
- Abkehr, Minimierung von „Firefighting“ seitens der Führungskräfte
- Weniger Überraschungen und Belastungen im Tagesablauf
- Entwicklung der Bereichsleiter und Teamleiter hin zu proaktivem Führen
Total Quality Management (TQM) bezeichnet die durchgängige, fortwährende und alle Bereiche eines Unternehmens erfassende, sichtende, organisierende und kontrollierende Tätigkeit. TQM heißt die Marktführerschaft für alle Produkte und Dienstleistungen des Unternehmens anzustreben. Es fokussiert sich auf Produkte und auf Dienstleistungen und bezieht die Mitarbeitenden aller Bereiche und Ebenen ein. Es unterstützt Selbstorganisation und Selbststeuerung und überlässt die Qualitäts- Verantwortung dem Team. Das Agile QM ist hochgradig kundenbedürfnisorientiert. Es versteht ganz genau was die Mitarbeitenden und Führungskräfte benötigen, um die Ziele zu erreichen und Ihre Aufgaben zu erfüllen. Es schafft Rahmenbedingungen und Regelwerke und unterstützt, um bestmögliche Produkt- und Prozessqualität zu erlangen.
Unser Leistungsspektrum bei TQM umfasst Folgendes:
- Kennzahlenbasierte Prozessanalyse
- Organisationsanalyse
- Informationsstrukturanalyse (ISA)
- Tätigkeitsstrukturanalyse
- TQM Begehungen
- Gemba Walks
- Trainings und Coaching
Ziel der Kanban-Methode ist es, die Wertschöpfungskette auf jeder Fertigungs-/Produktionsstufe einer mehrstufigen Integrationskette kostenoptimal zu steuern. Es ist ein System zur Steuerung des Materialflusses und der Produktion nach dem „Pull-Prinzip“. Dabei werden sogenannte selbststeuernde Regelkreise eingesetzt, um die Materialversorgung zu gewährleisten. Das Kanban-System sorgt dafür, dass alle notwendigen Materialien am entsprechenden Produktionsort bereit liegen.
Unser Leistungsspektrum bei der Einführung von Kanban umfasst Folgendes:
- Beratung bei Einführung und Umsetzung
- Begleitung und Moderation bei der Etablierung
- Unterstützung bei der Analyse und Neugestaltung von Prozessen
- Beratung und Unterstützung bei der Einbindung notwendiger Hilfsmittel
- Durchführung von Schulungen
- Enge Zusammenarbeit mit Ihren Fachleuten in jeder Phase der Integration
- Probedurchlauf mit Pilotprojekt(en) und anschließender Wirksamkeitsüberprüfung
- Wir bieten komplette Projektbegleitung und Dokumentation der Ergebnisse
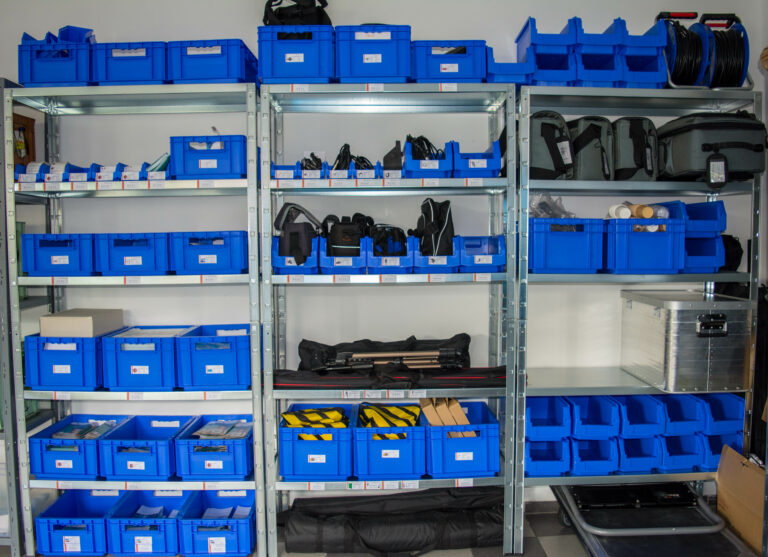
Referenzobjekte
Ihr Ansprechpartner
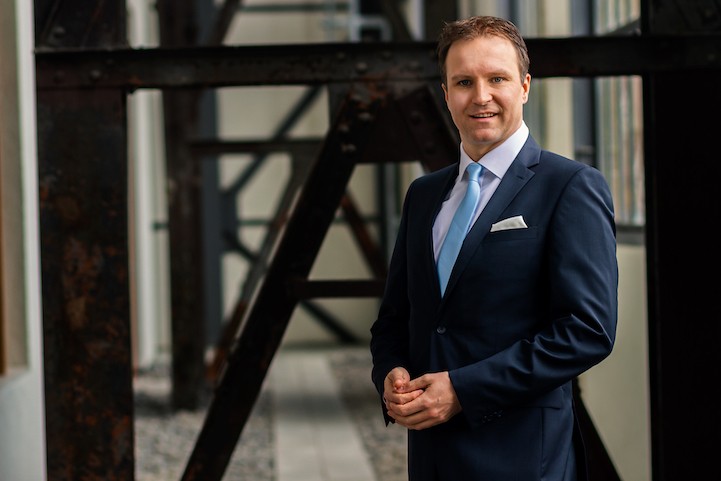
B.BA. Heiko Hüsemann
Manager OPEX
LEANNOVA GmbH
Clara-Eylert-Str. 4
49809 Lingen (Ems)